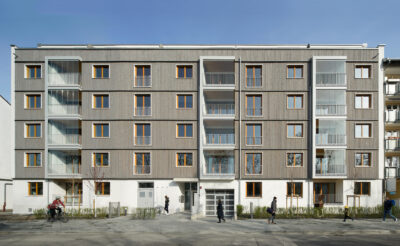
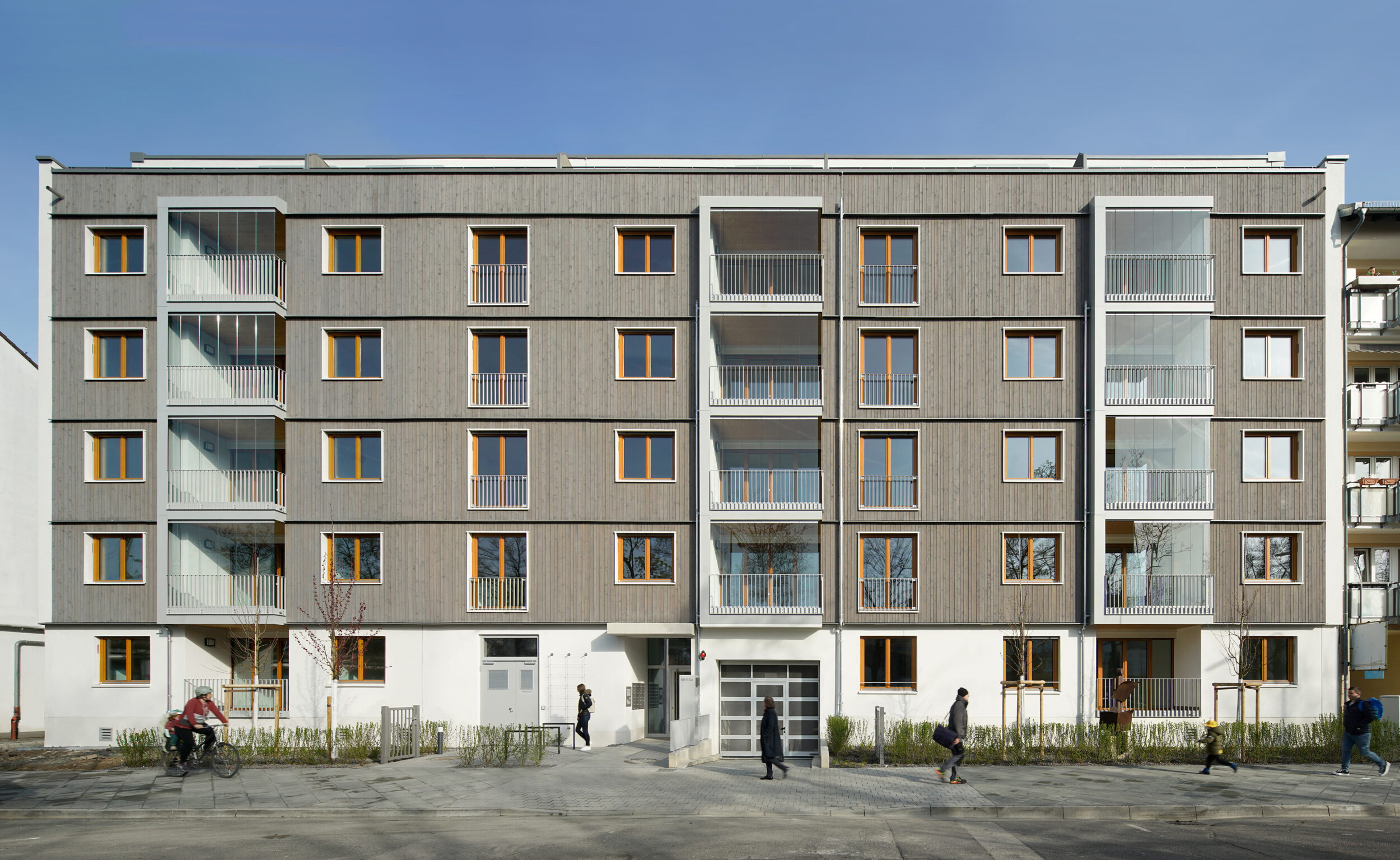
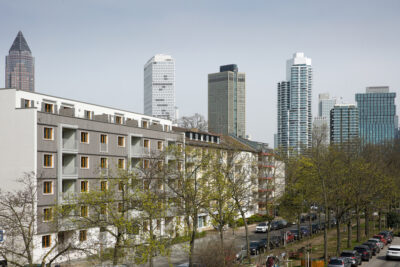
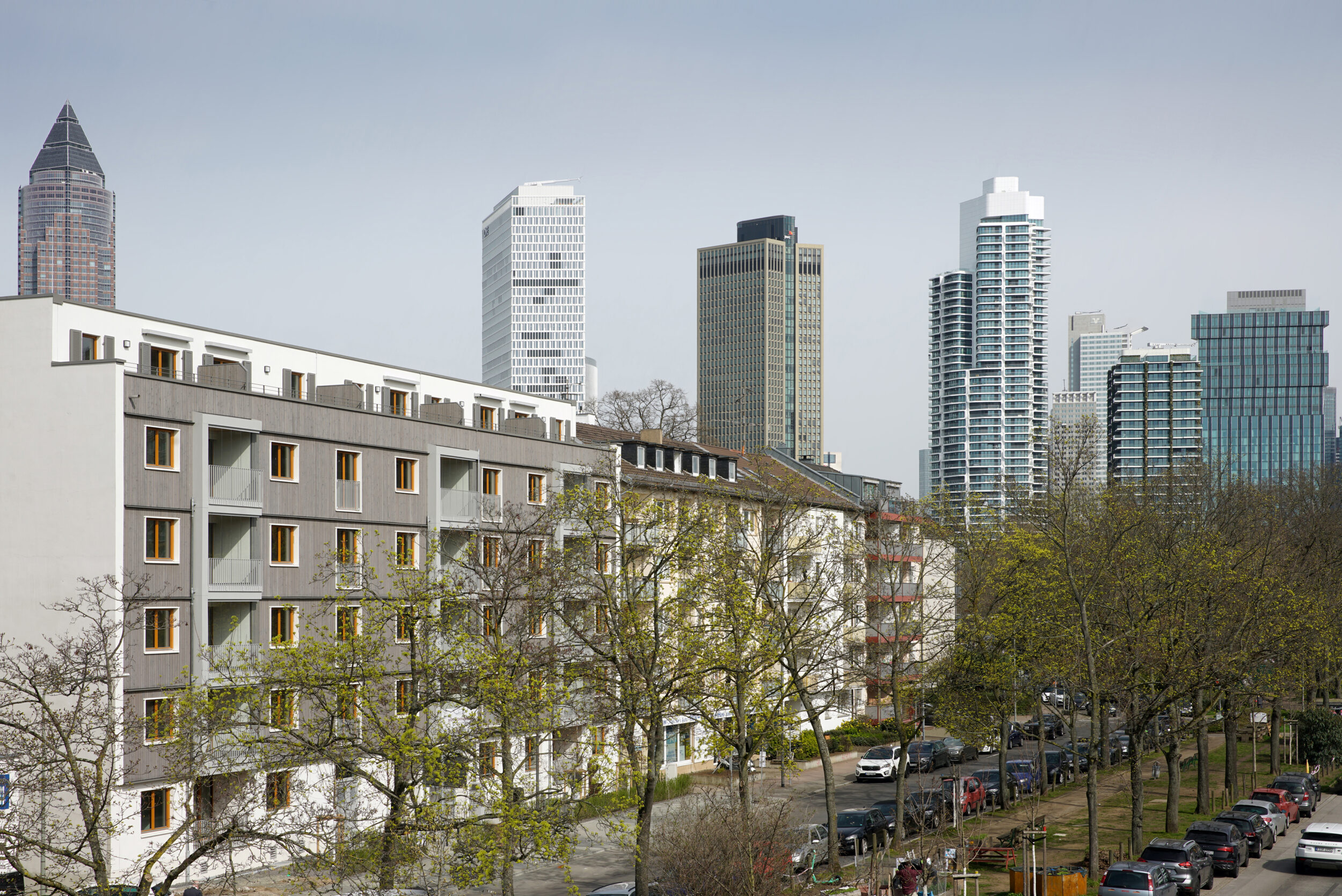

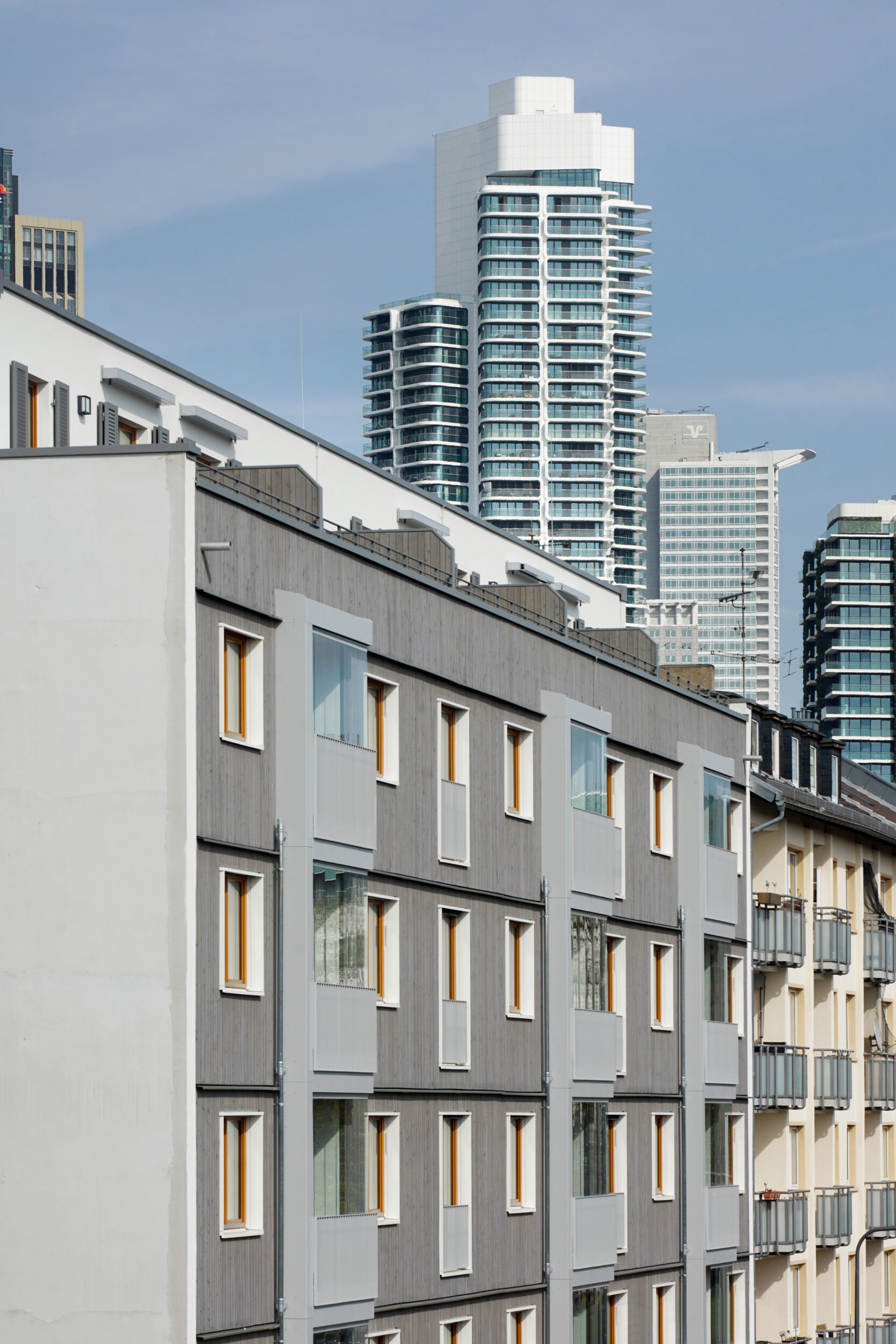
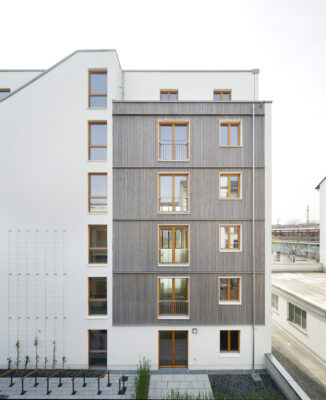
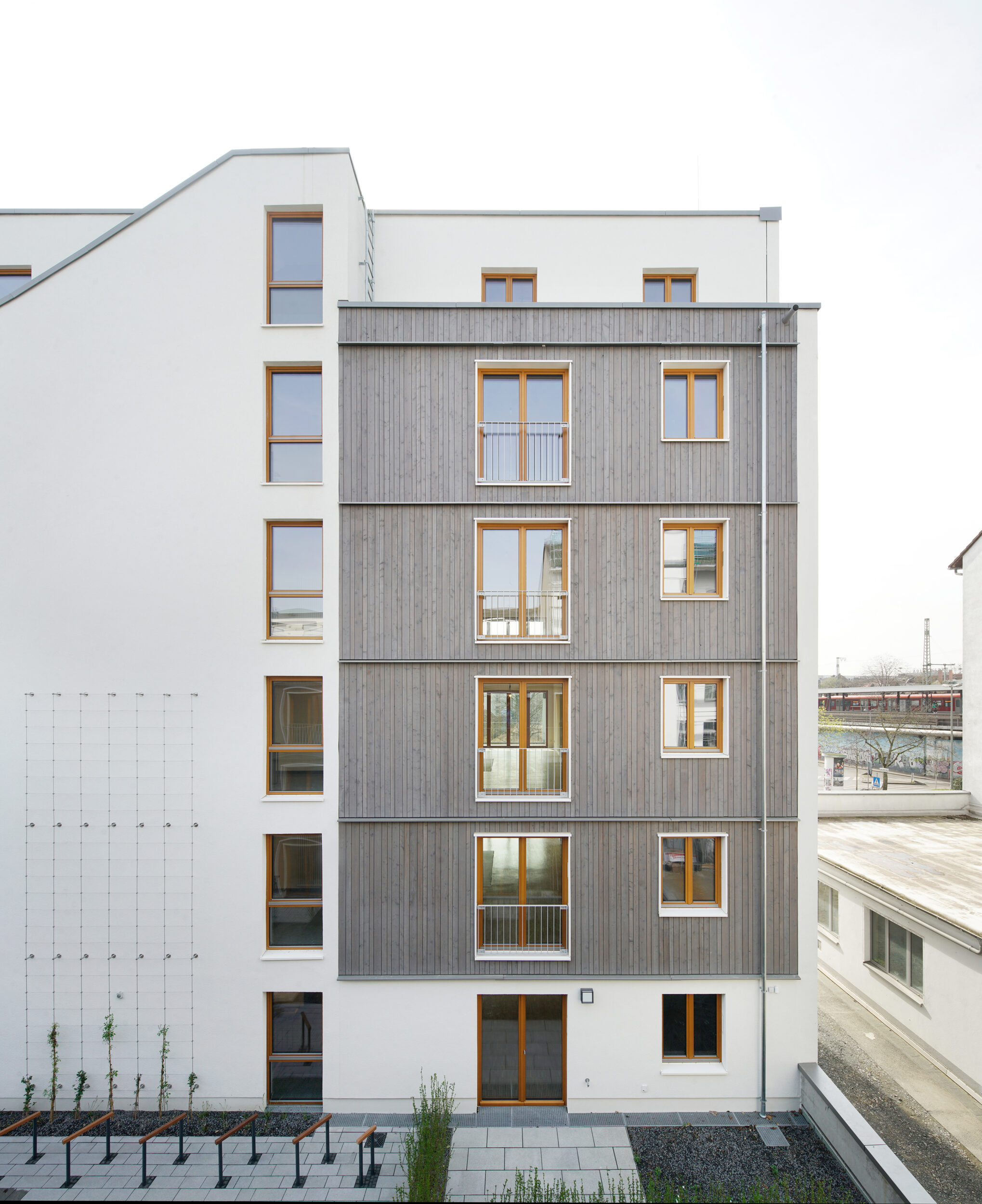
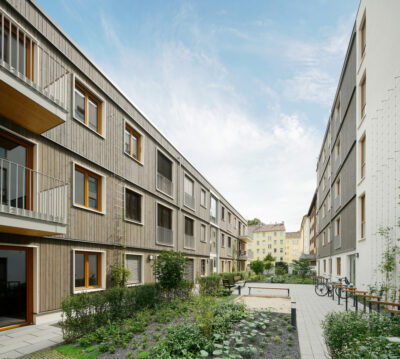
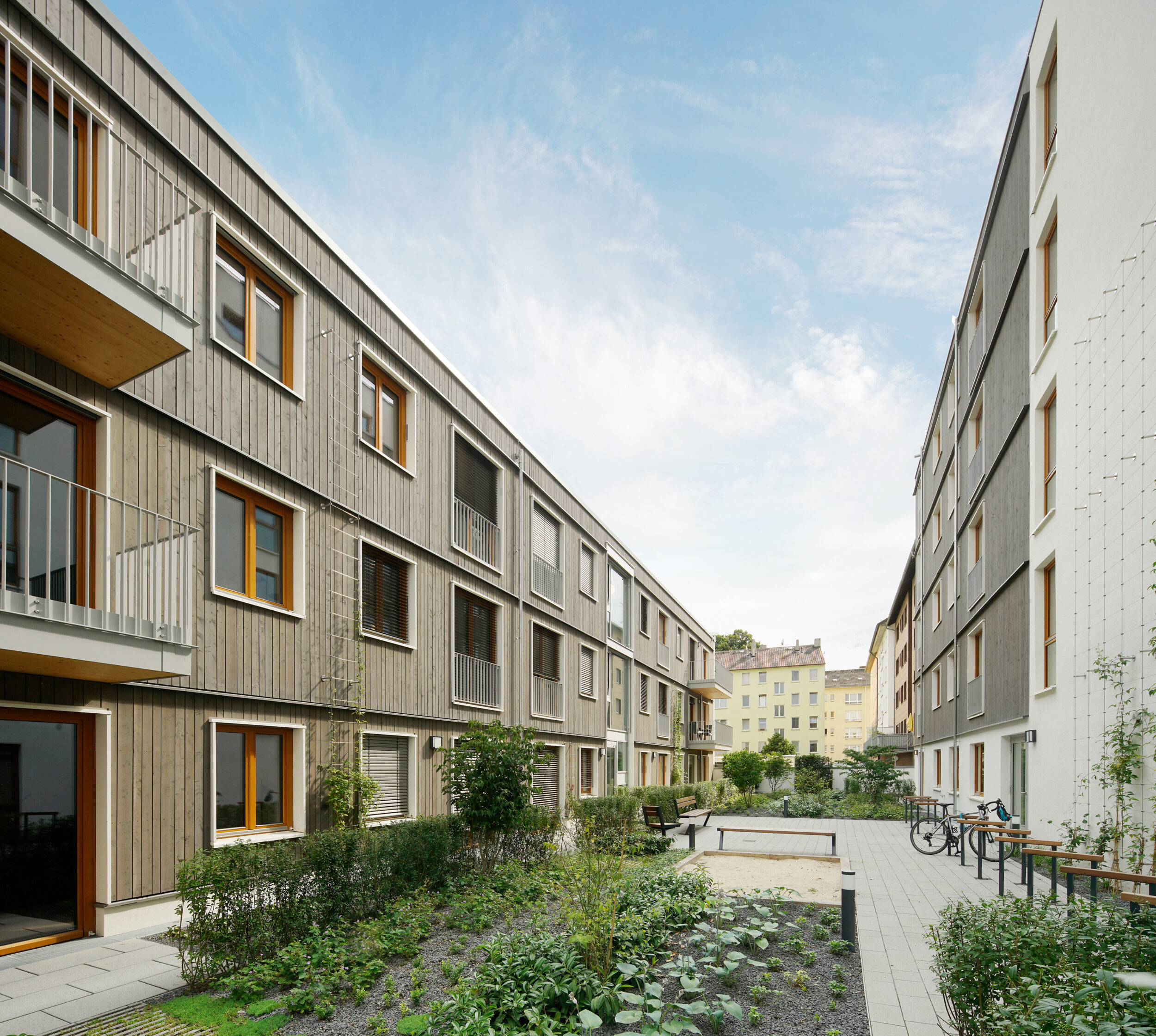
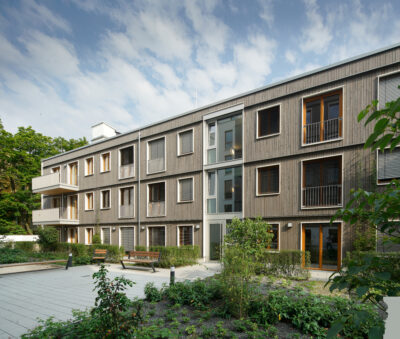

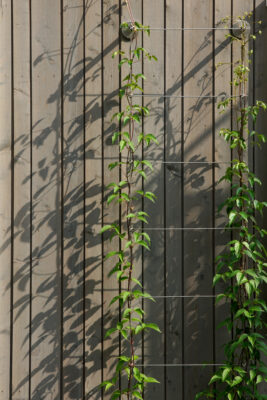
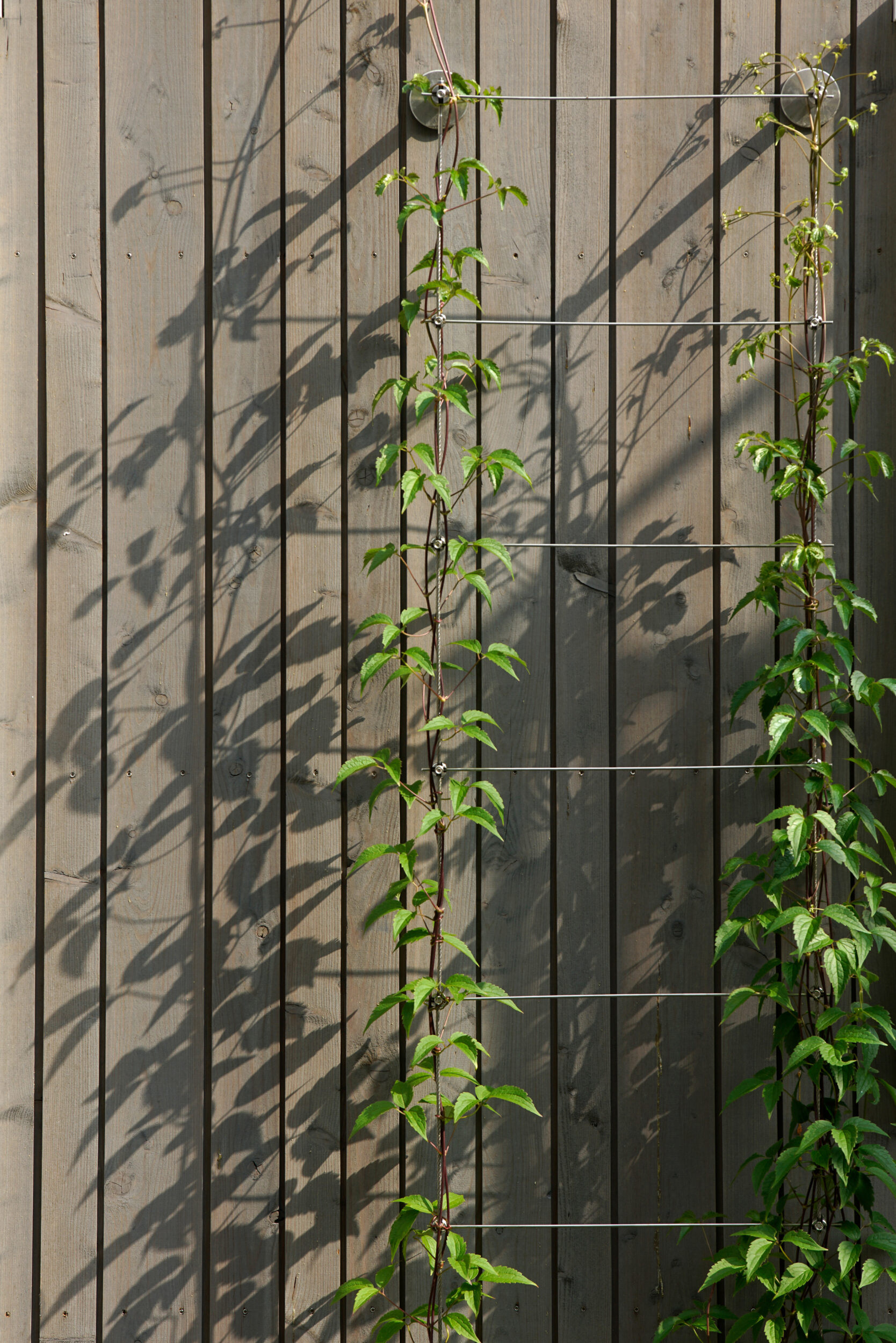
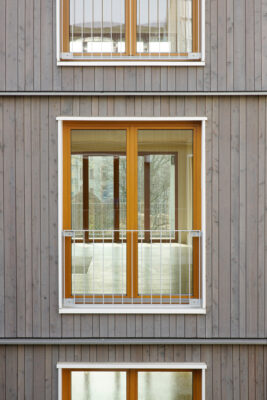
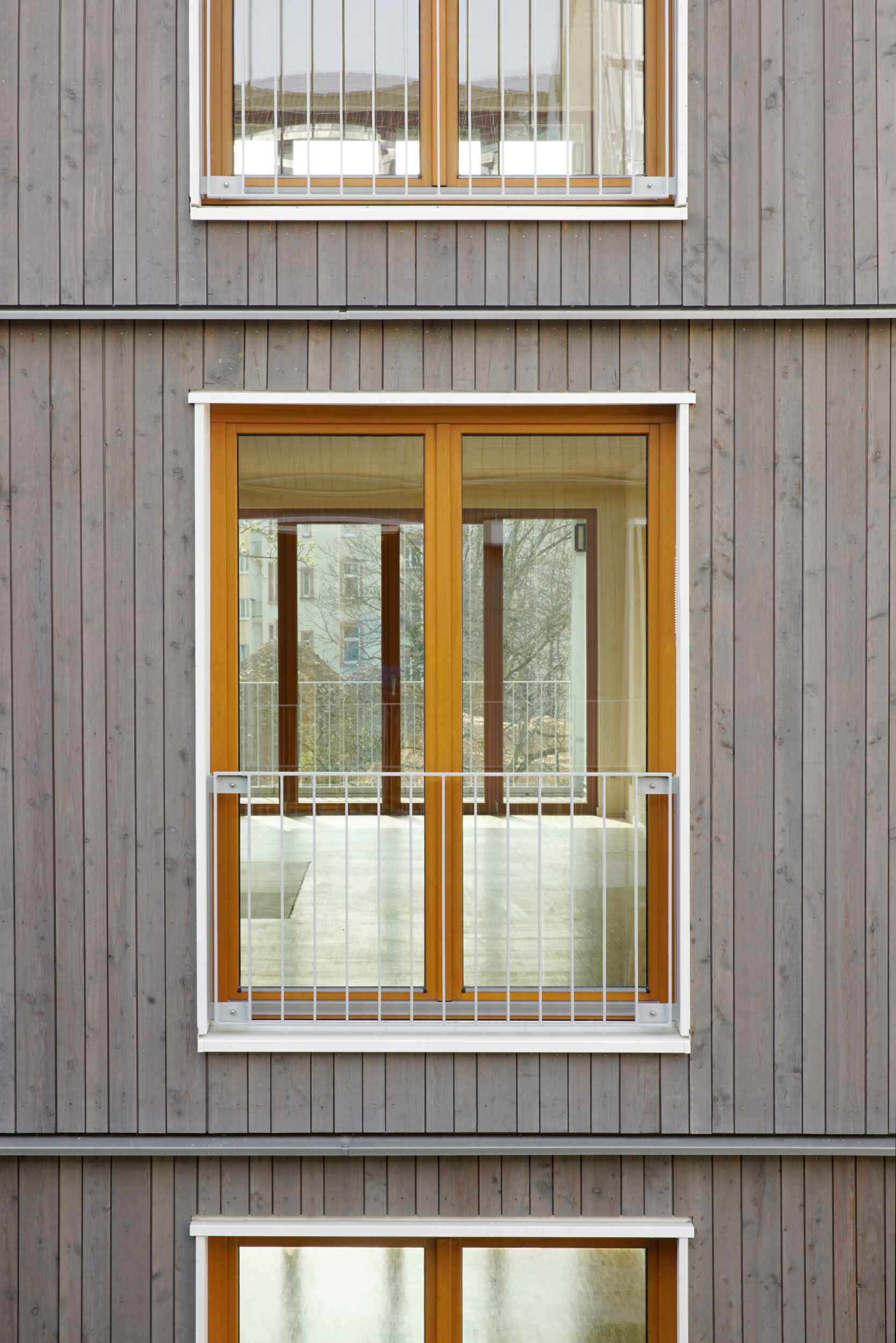
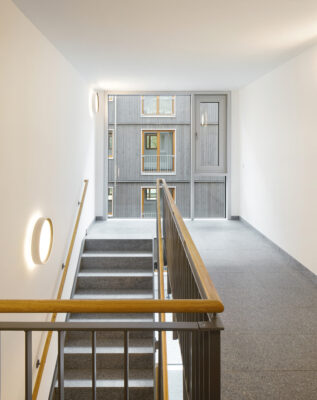
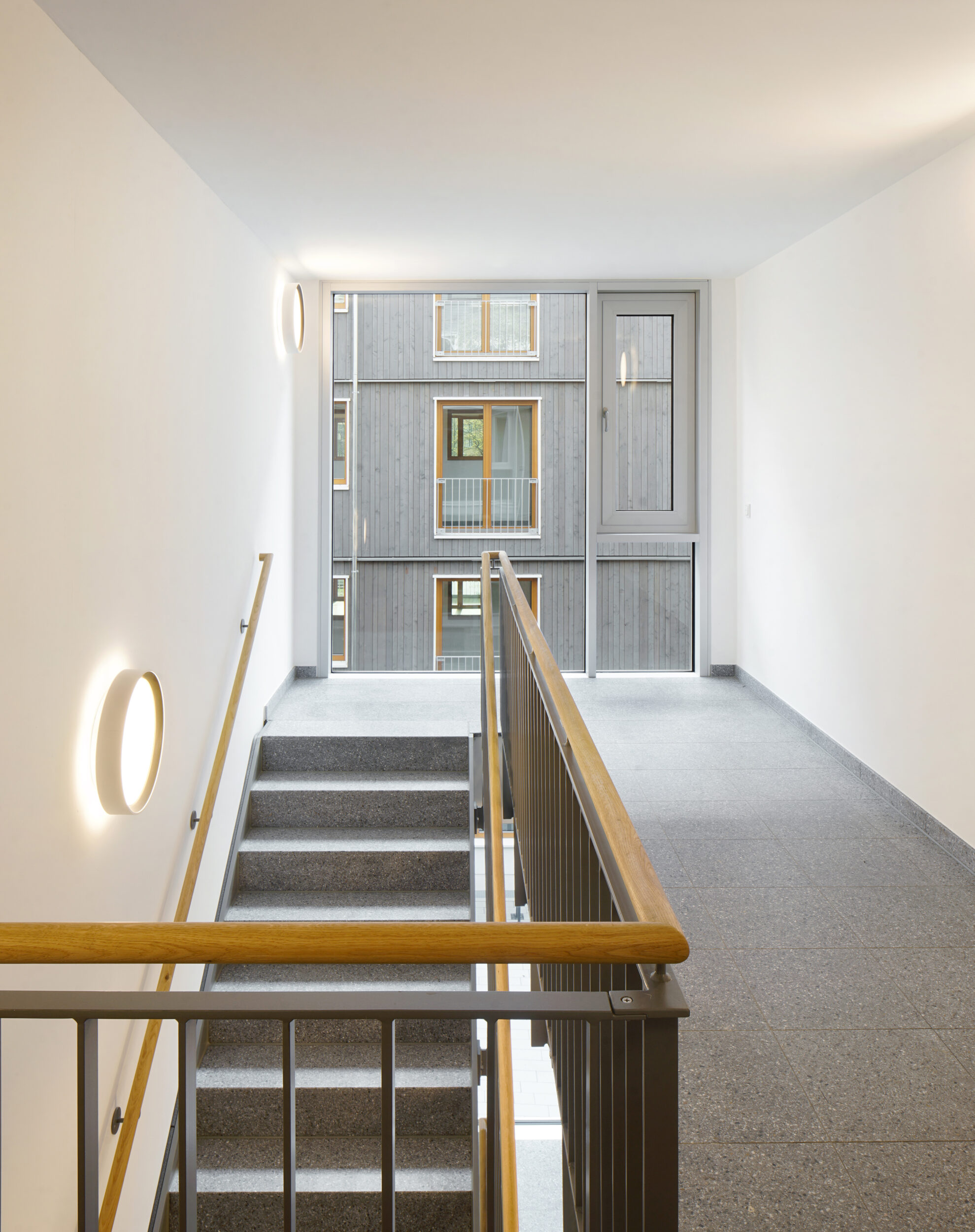
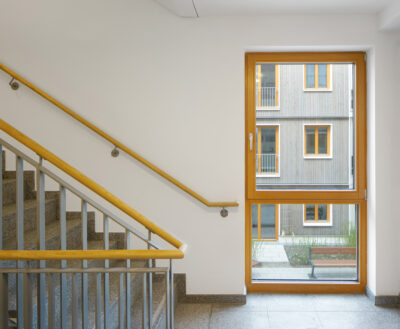
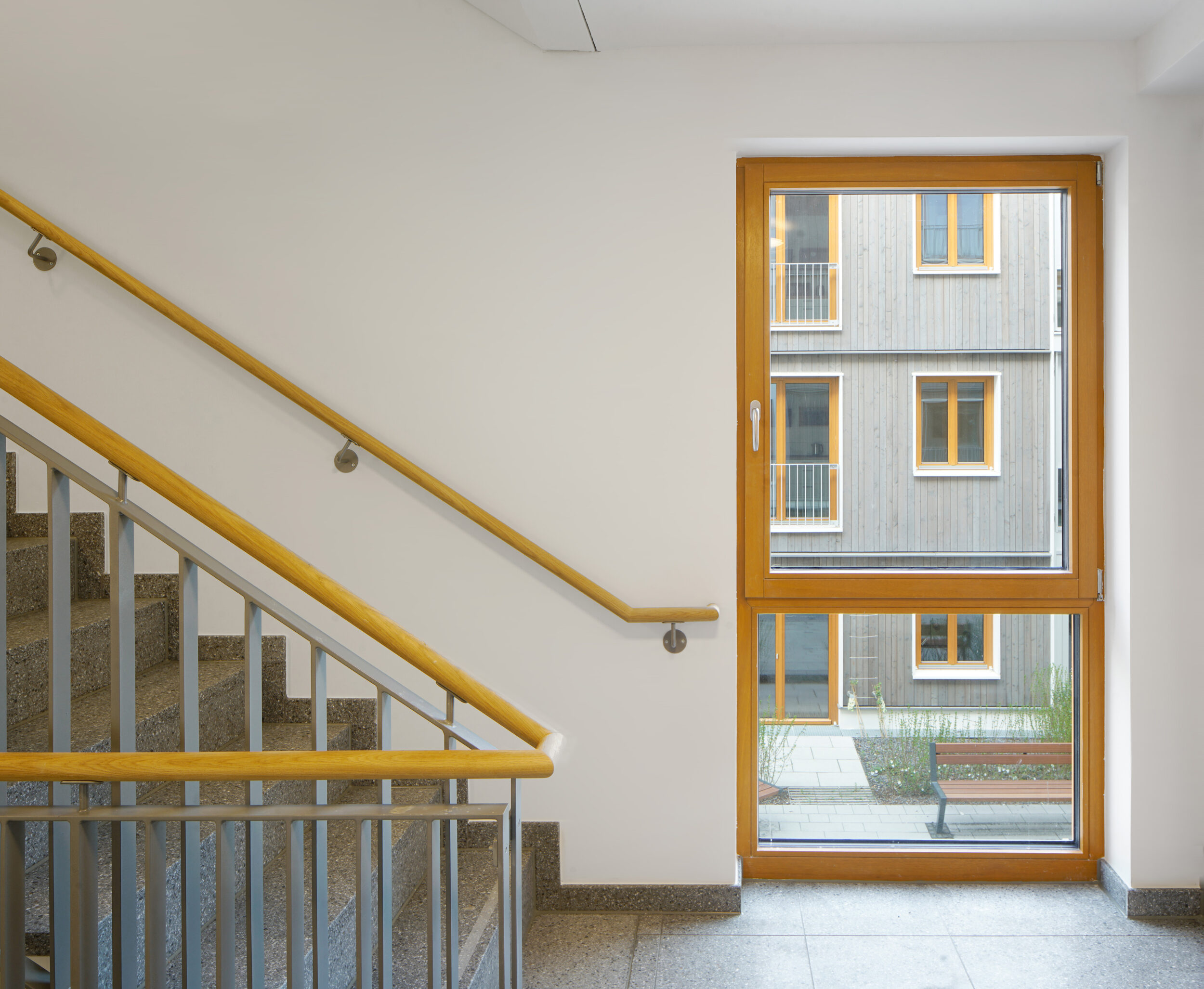
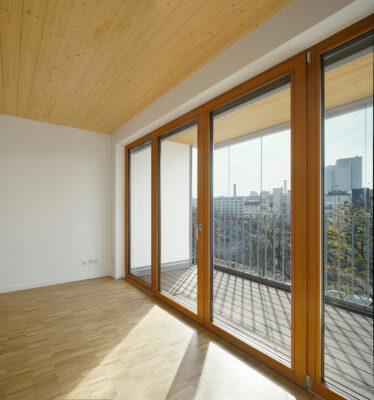
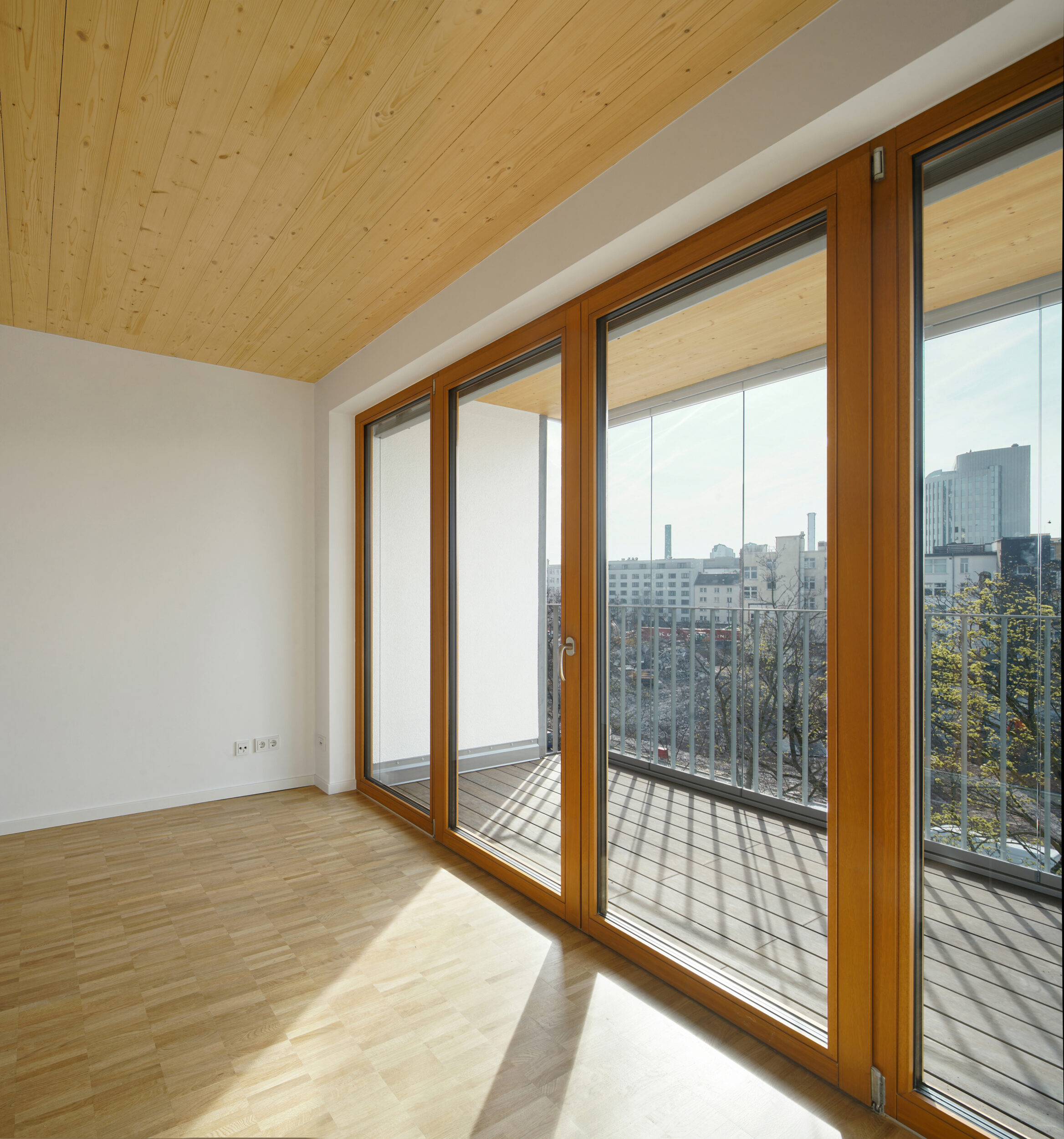
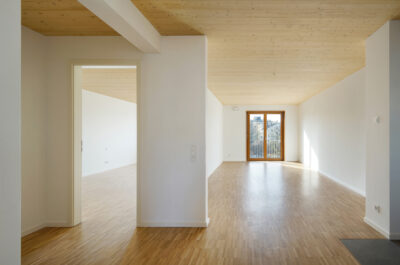
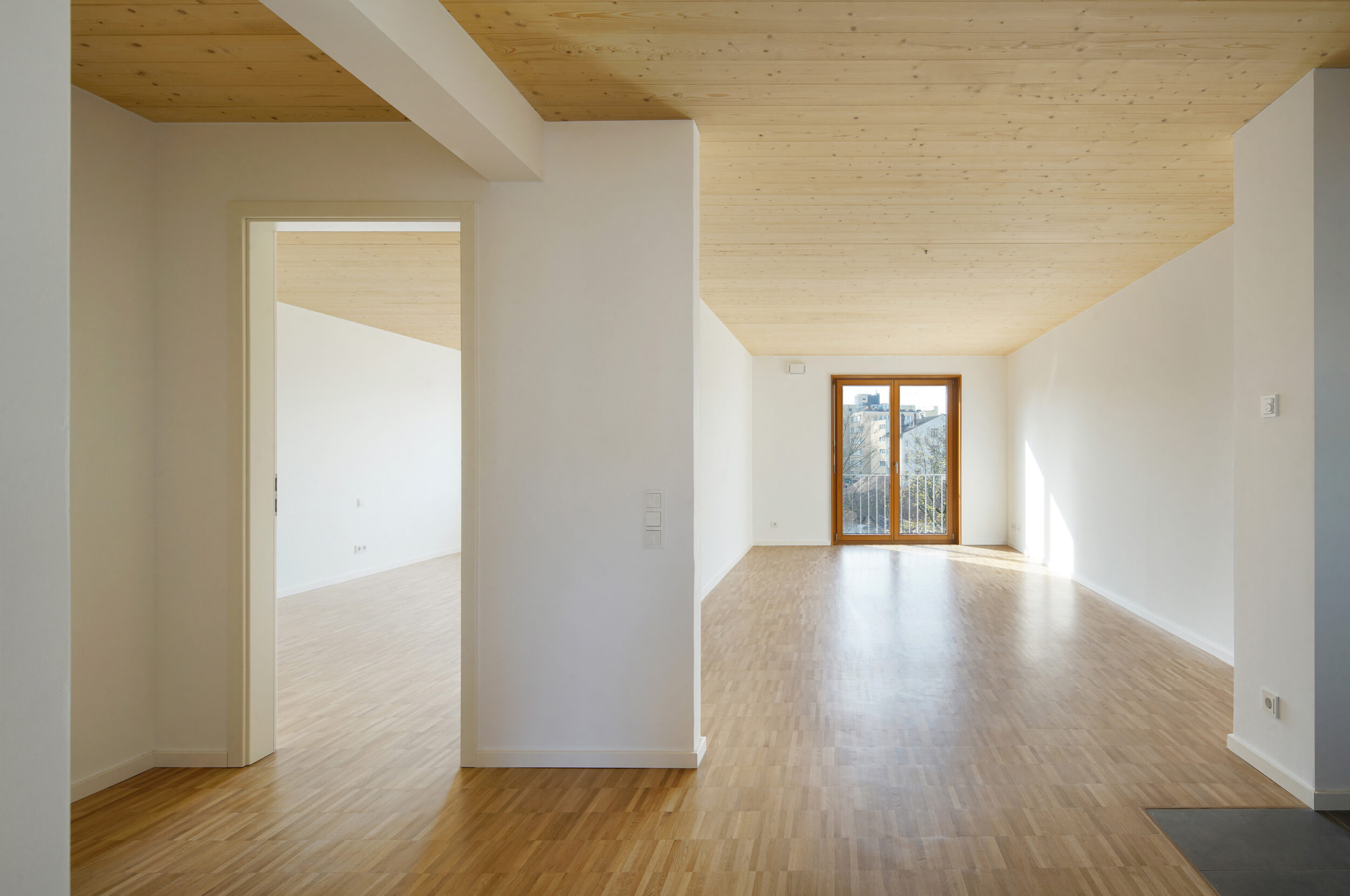
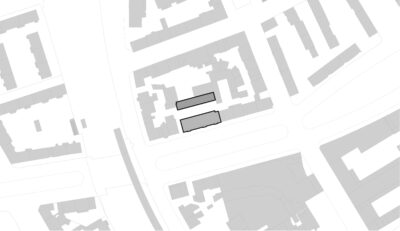
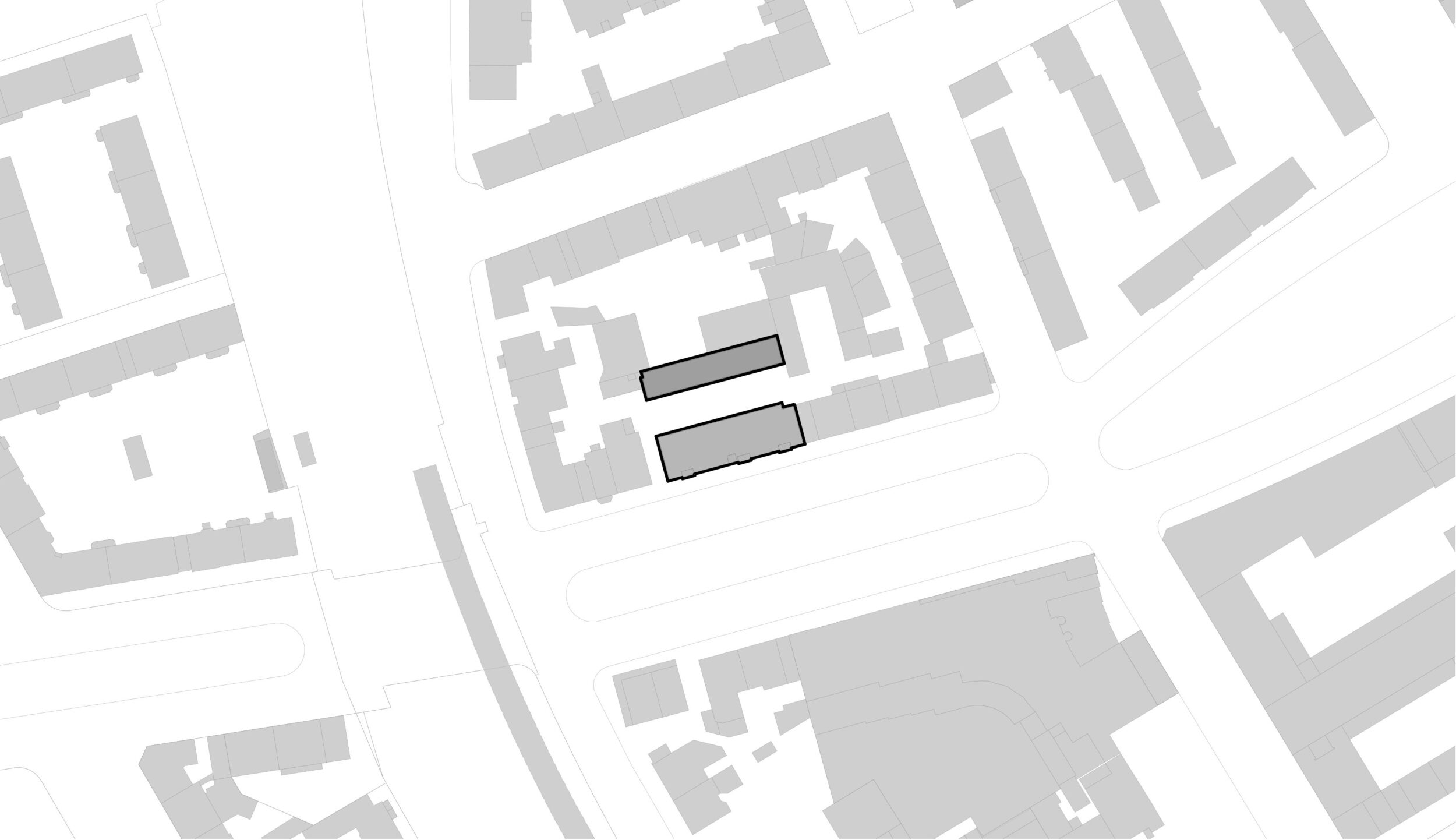
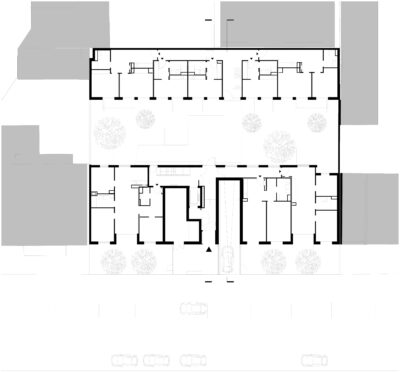
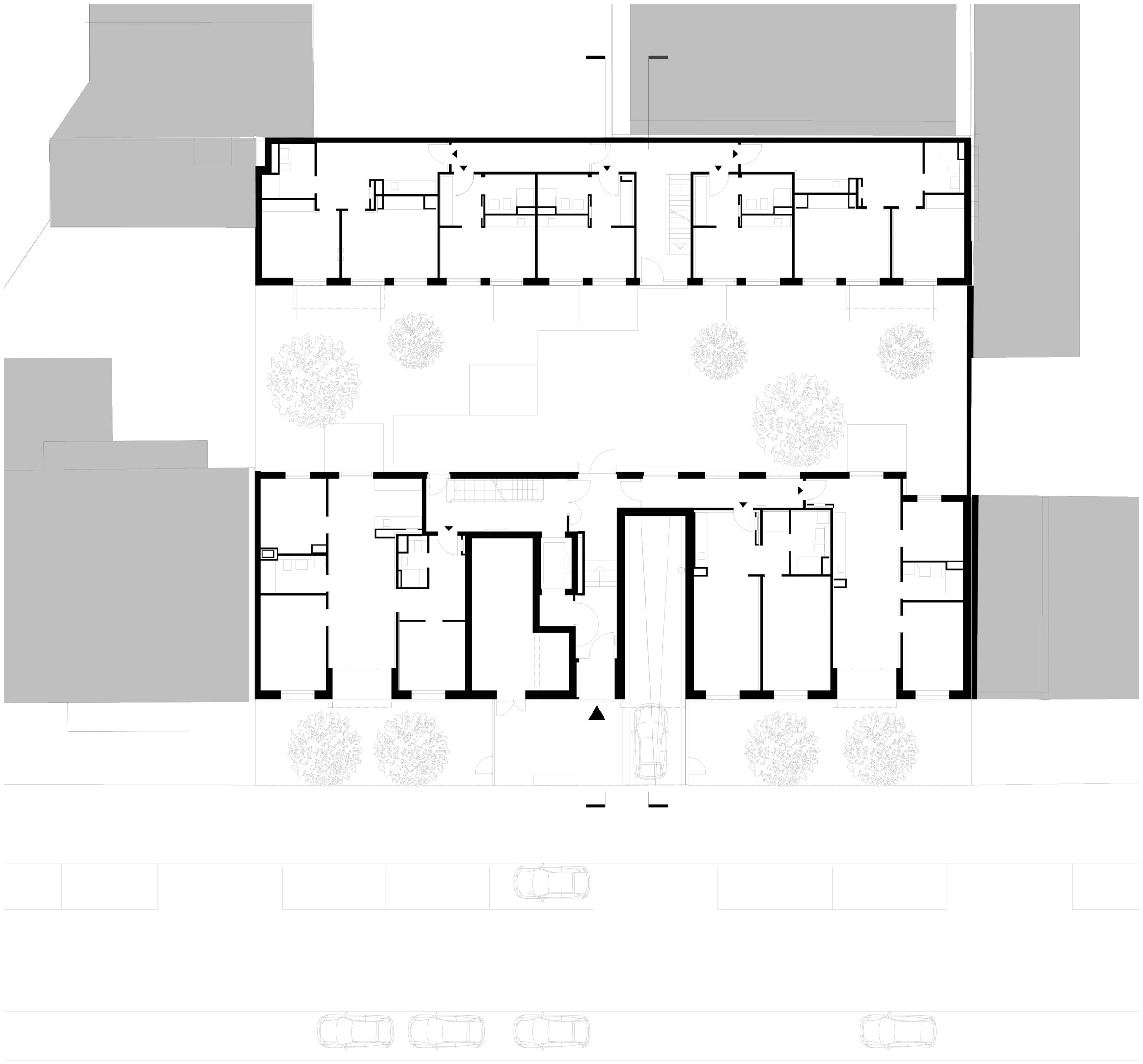
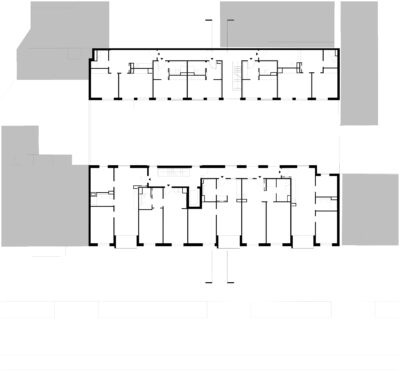
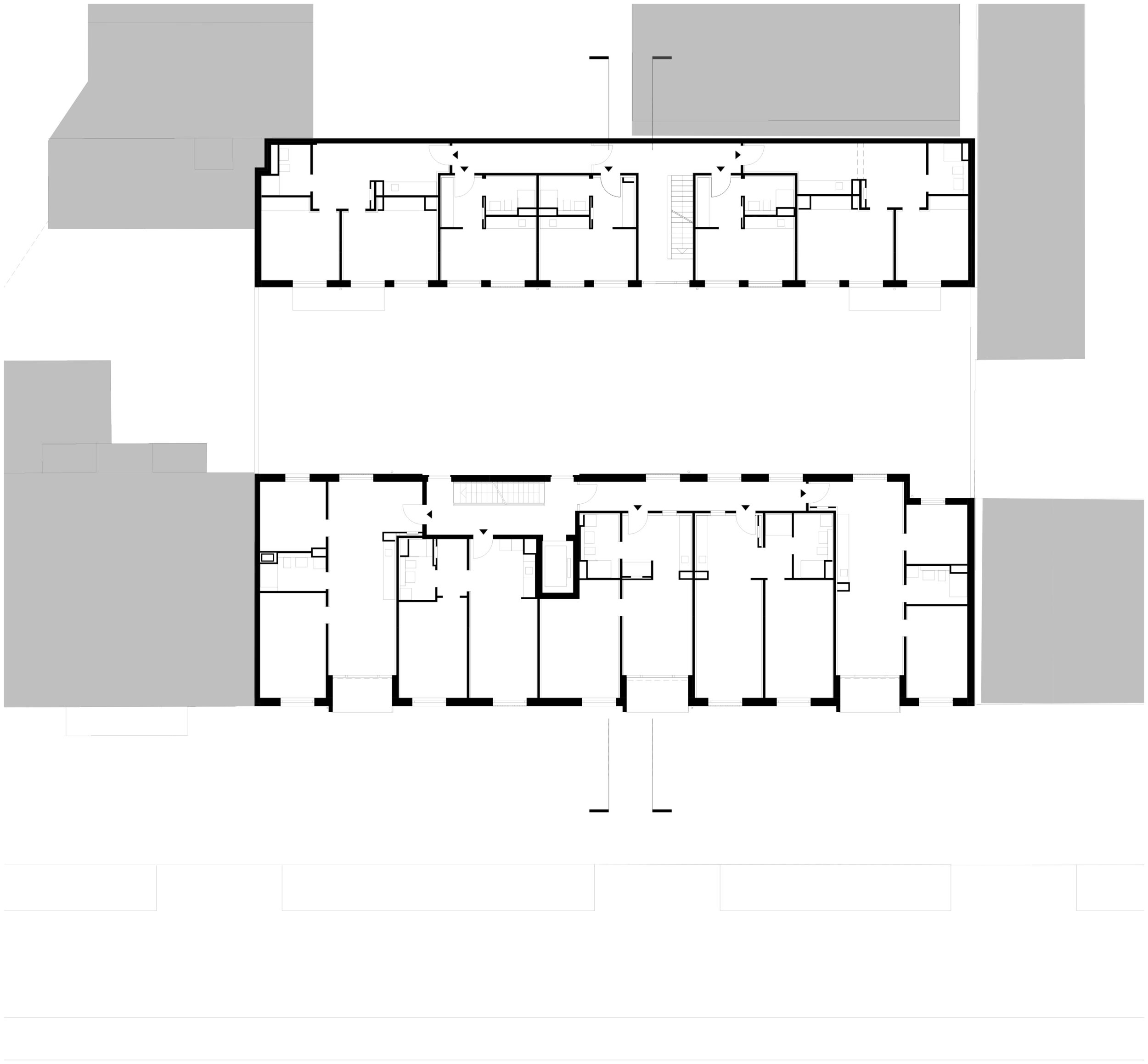
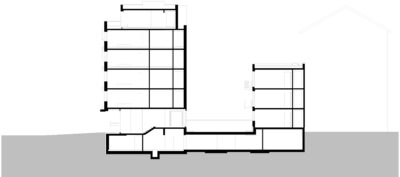
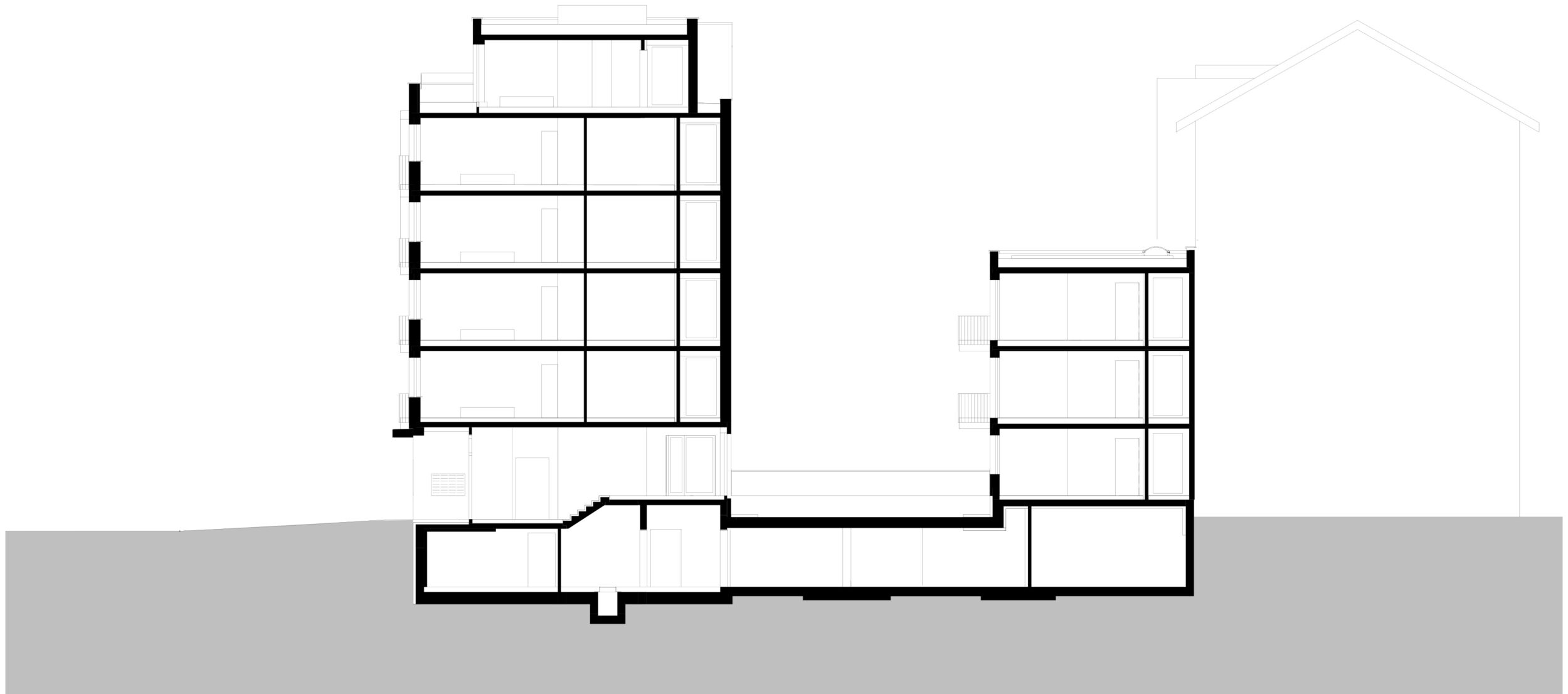
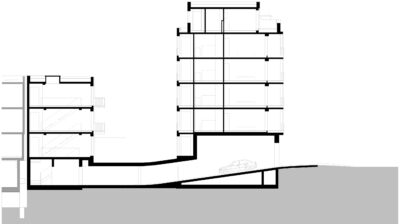
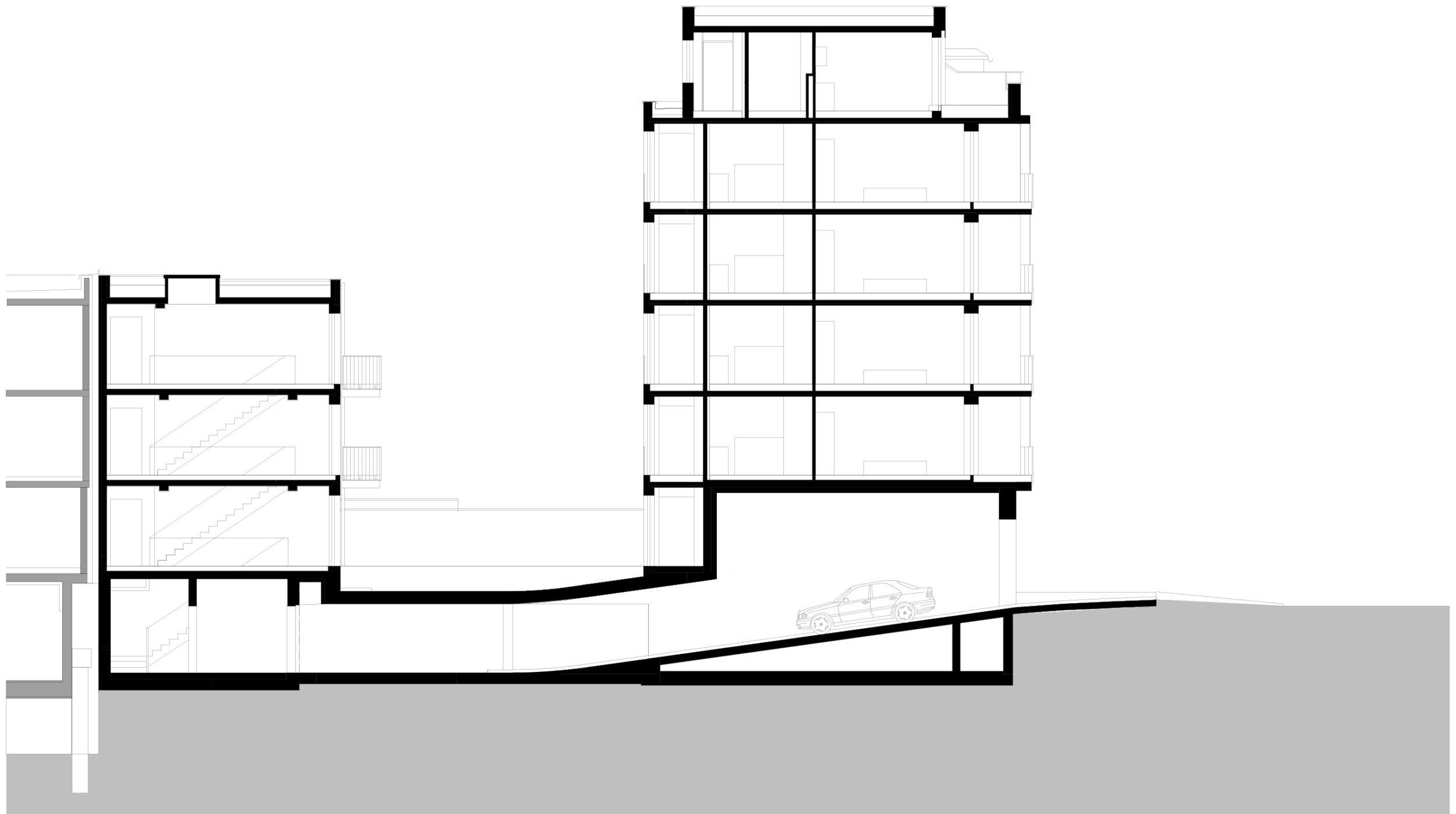
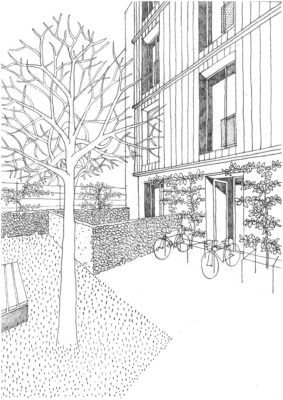
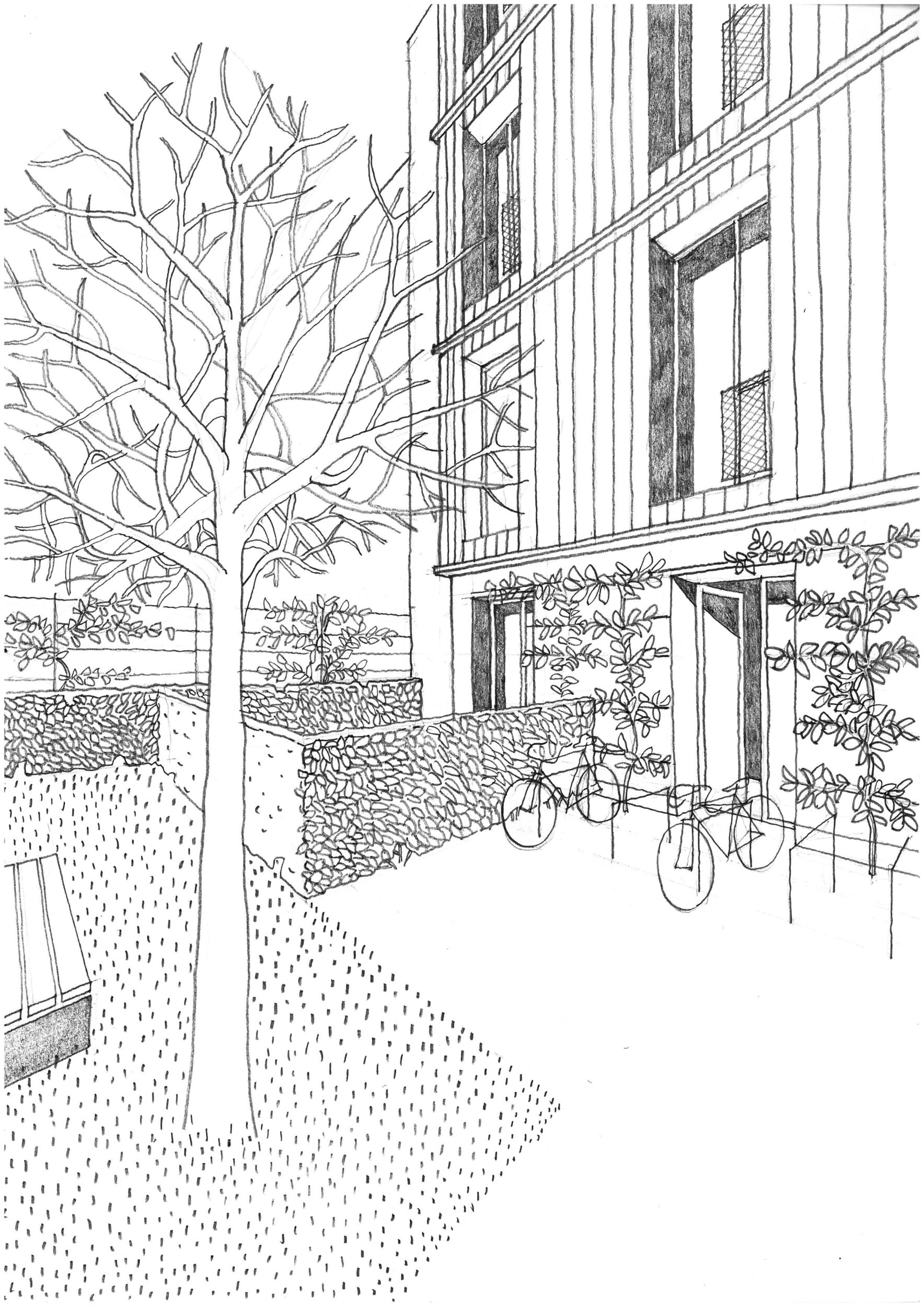
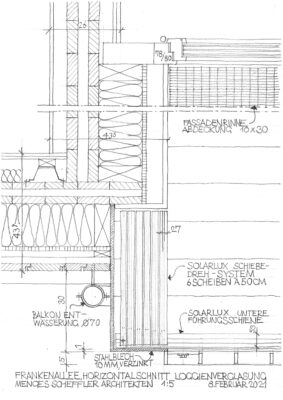

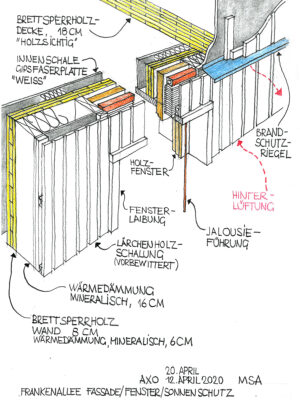
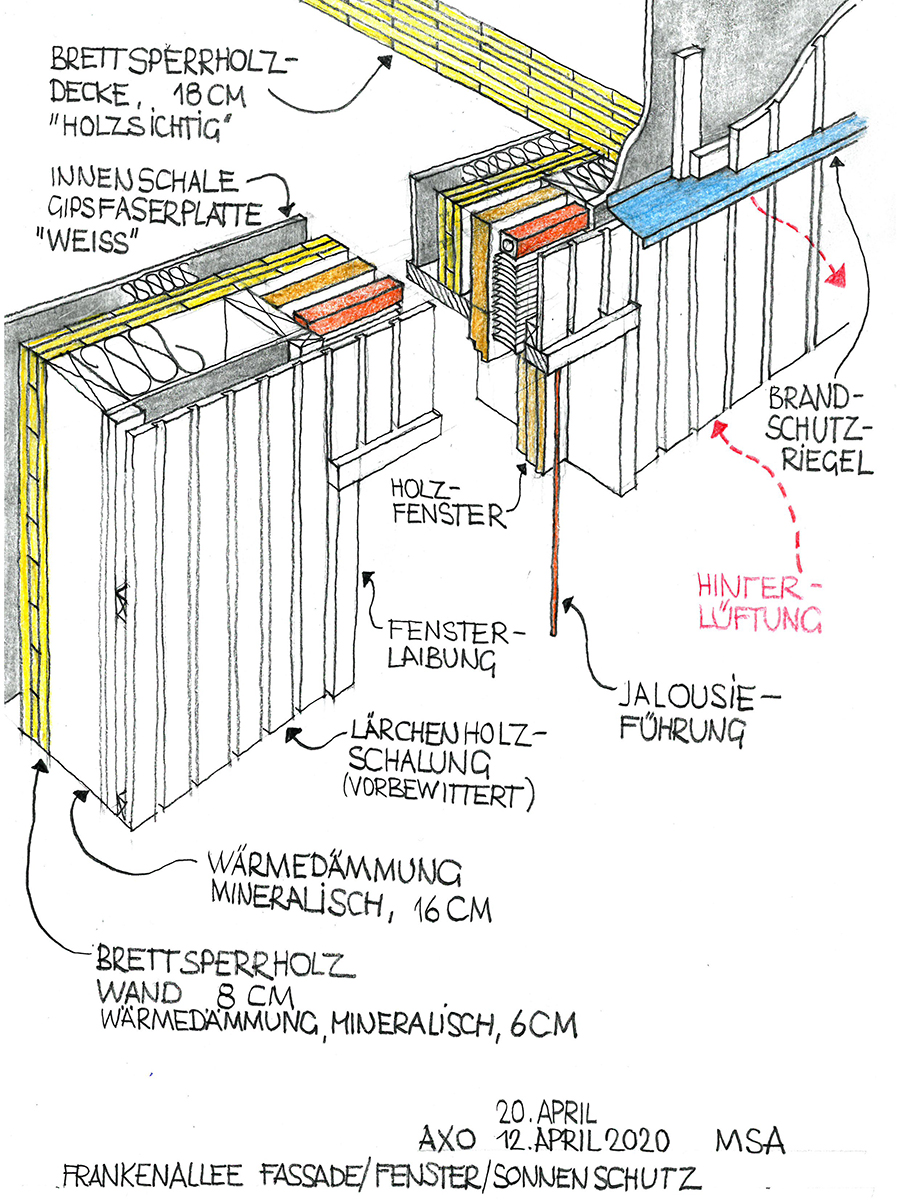

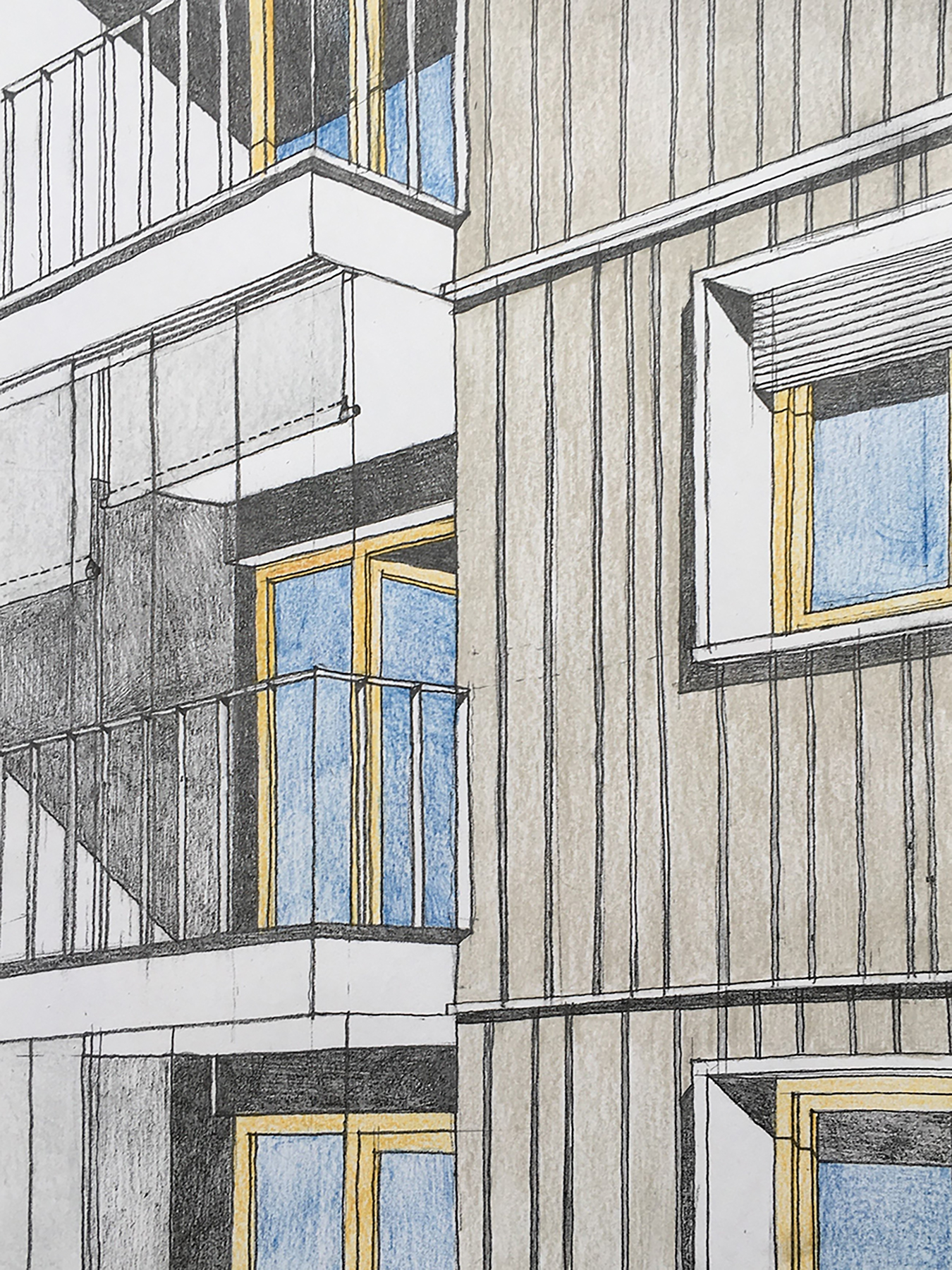
FAZ FRANKENALLEE
New construction of two apartment blocks
Location | Frankfurt am Main |
Client | Frankfurter Allgemeine Zeitung GmbH |
Floor Area | 4.545 m² |
Units | 43 |
Completion | 2023 |
Procurement | Competition, 1st Prize |
Phases | 1–9 |
In the heart of Frankfurt, just a two-minute walk from the Galluswarte station at Frankenallee 68 and 68a, two modern apartment buildings in solid timber construction were completed in spring 2024. The ensemble consists of a front and a rear building with a total of 43 apartments that enclose a green inner courtyard. With five full storeys and a staggered storey, the front building blends into the existing Frankenallee street. With three full storeys, the rear building matches the height of the courtyard building on Koblenzer Strasse and is directly adjacent to it.
Even though a wooden façade on a six-storey building is still very unusual at present and unique in residential construction in Frankfurt, the new building blends naturally into its surroundings. The construction is based on cross-laminated timber, which forms the load-bearing elements for the ceilings and walls. Only the parts of the basement in contact with the ground and the staircase of the front building are made of reinforced concrete. The walls of the front and rear buildings adjacent to the neighboring buildings were constructed as fire walls in sand-lime brick or aerated concrete block. The apartment partition walls and the partition walls are designed as load-bearing cross-laminated timber bulkheads on which the cross-laminated timber ceiling elements rest.
By applying for a project-related building permit (vBG), a residential building in building class 5 in timber construction, which was previously not possible in Hesse, was realized. The increased sound insulation requirements demanded in residential construction were met in the main areas, as were the extended fire protection requirements.
Despite extremely high external noise levels of 80dB caused by ICE and freight traffic at the nearby Galluswarte station, it was also possible to implement very good sound insulation requirements on the external façade in timber construction.
The façade is designed with vertical, rear-ventilated tongue-and-groove cladding. The local larch boards used vary in width and are repeated in an irregular rhythm. The pre-greying was created using a mineral/silicate-based glaze. Fire protection bars structure the façade and prevent the spread of flames on each storey.
The outdoor seating areas facing Frankenallee are designed as loggias. Due to the proximity to the tracks, the loggias can be closed with glass baffle plates for sound insulation. When open, the baffle plates are »parked« in a niche and can be easily extended from there using a sliding and rotating system.
The apartments are all pleasantly bright and have a distinctly homely character. This is enhanced by the material combination of oak mosaic parquet flooring, the wooden ceiling soffit of the load-bearing cross-laminated timber, the white walls and the reddish-brown solid wood windows. The large windows add to the sense of comfort.
The open space between the front and rear buildings serves as a green oasis. Here, residents can find a spot in the sun or shade, shielded from the hustle and bustle of the street and the nearby S-Bahn station, and wind down the day among shrubs, flowers and trees, celebrate a children’s birthday party or simply read a book.
In addition to the green inner courtyard design, the green facades on the stairwell, the front gardens and the green roofs (with rainwater retention) contribute to a more pleasant microclimate.